Manufacturing data collection and analytics with IoT wearables
AGC uses IoT wearables to collect manufacturing data from factory workers
ABOUT
Easier to acquire and analyze data for improvement
Asahi Glass Co., also known as AGC, have been collecting and analyzing data from their factory for some time now. However, most of the analysis has been done by work supervisors and engineers taking pictures and videos of work and using paper and stopwatches.
The data that is collected is often stored in the personal computer of the person in charge at the site, and is often analyzed with Microsoft Excel rather than a common analysis tool.
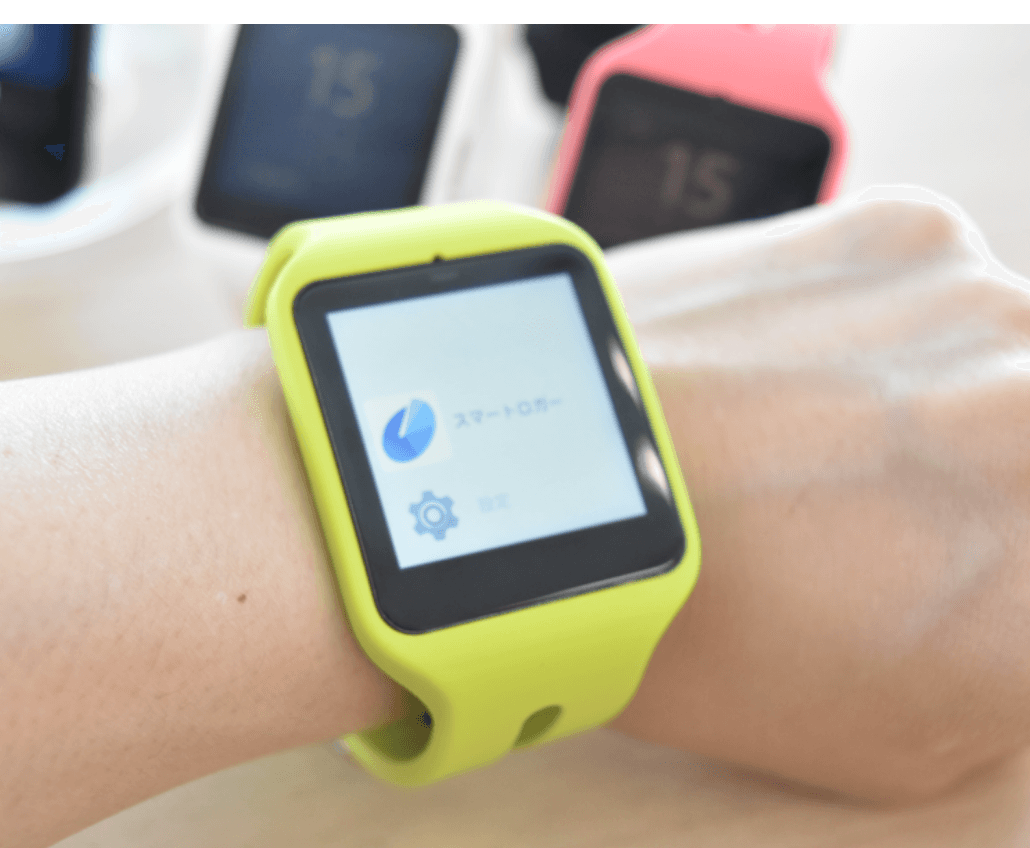
CHALLENGE
AGC found that all three steps of their process (data acquisition, analysis and improvement) required significant improvement, especially data acquisition and analysis, which they found they were spending too much time on.
They believed that there had to be an easier way to consolidate all of the data kept at the site and provide an analysis that could efficiently and effectively use their findings to improve operations.
SOLUTION
AGC developed a work dynamic analysis solution called Smart Logger in collaboration with CEC Corporation. They provided each factory worker and engineer with smartphones and wearable loggers (watches or glasses) so they could easily gather work data.
The data that was collected would be accumulated in the cloud using Soracom cellular connectivity, and would be analyzed and visualized with their business intelligence tool. From there, the factory supervisor could analyze the findings and take action to improve operations.
By using IoT technology, AGC has been able to gather the data that they collected and consolidate it in one location. Analyzing the data using their BI tool enabled them to find new avenues for operational value and improvement, speeding up the innovation process drastically.
Work supervisors and engineers can now reduce the time they spend on data acquisition and analysis, freeing up more time to develop new ideas and imagine new improvements.
WHY SORACOM
AGC chose to power their IoT project with Soracom cellular connectivity because it was immediately operational and came at a reasonable cost. They could install SORACOM Air SIM cards directly into the smartphone or smart loggers and have the devices collect the data and send it to the cloud for analysis.
Soracom cellular connectivity was easy to obtain and cost-effective, enabling them to stay competitive while improving their processes.
Working with Soracom also allowed them to more effectively integrate their operations with the cloud, providing the flexibility they needed to scale their system configuration as analytics arrived.
AGC uses SORACOM Beam to encrypt the data that they collect, as well as manage and grant authentication. This provides AGC with the ability to facilitate a connection from the devices to the cloud without giving up device-side authentication.
In addition, with AGC owning overseas factories as well, they appreciated that Soracom cellular connectivity could be put to immediate use overseas as well.
Services in use
• SORACOM Air: smart connectivity for IoT
• SORACOM Beam: IoT protocol conversion
SYSTEM CONFIGURATION
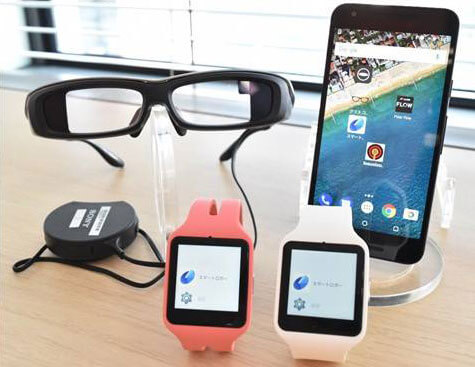
FUTURE PLANS
AGC believes companies need to incorporate new technologies to improve reliability and stability while providing improved usability to customers.
While the manufacturing industry has security barriers with highly confidential data, they emphasize the importance of data and analytics, and recommend that these barriers can be overcome with secure IoT technology and the cloud.
AGC is planning to use their smart loggers with office workers, expanding the analytics that they gather to other divisions of their corporation.
While the manufacturing industry worries more about waste management and production issues, AGC feels that the focus with office workers will revolve around value-added time.