Industrial IoT
Intelligent power plant management - IHI
ABOUT
Keeping power plants at peak operating efficiency, anywhere in the world
IHI Corporation is a global manufacturer of heavy-industrial equipment. The company’s strategic business units work around the world to deliver everything from industrial and agricultural systems to aerospace products and even nuclear reactors.
IHI’s power generation team provides comprehensive services across the complete lifecycle of gas turbine power plants from design and manufacture to installation and maintenance.
Because these power plants are often located in remote areas, IHI has pioneered a variety of monitoring and maintenance capabilities. IHI’s first remote monitoring system was introduced in 1995. Today this remote monitoring service uses an always-on, secure wireline (copper or optical) connection. The one-way link, from plant to monitoring site, is secured through IHI proprietary protocols. The transmitted data is used for real-time diagnosis of the power plant turbines and related equipment using continuous analysis of live data from the field.
Photo courtesy of Glow SPP 11, Thailand
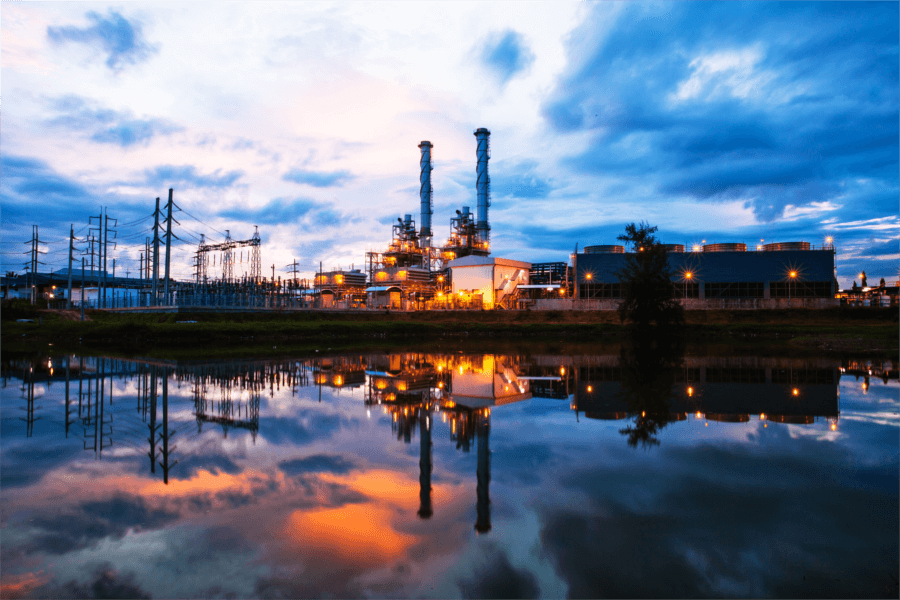
CHALLENGE
Ensuring a secure, 2-way connection between IHI and customer systems
While every power-plant component is set up at installation for optimal performance, normal wear, passage of time and seasons in rugged environments require periodic adjustment to ensure continued optimal operation.
When remote monitoring data indicated repair or adjustment was required, IHI would often send a team to the site to make corrections. To improve its service offering, IHI looked for a system that would allow service technicians to adjust plant equipment remotely. Until recently, however, given the potential impact to a region should a power plant be compromised, the risk of accessing customer systems over the Internet was long deemed to be too high to justify the benefit.
SOLUTION
A secure, global wireless data channel
For IHI, the Soracom Gate private networking service represented the ideal solution. Soracom Gate is a secure, on-demand cellular link that supports remote control of equipment parameters without sending data over the public internet. This prevents unauthorized access to IHI or customer systems.
Soracom Gate also offers compelling cost benefits. Unlike full-time connections required for real-time monitoring, the connection required for real-time adjustment is used relatively infrequently. This made Soracom’s pay-as-you-go fee structure a natural fit to minimize the cost of remote adjustments, and the ability to begin testing on a self-service basis with nearly zero upfront cost went a long way toward developing a proof-of-concept quickly for internal approval.
Because more than 50% of IHI’s gas turbine power plants are installed outside of their home market, Soracom’s global footprint made plant management simple from a business perspective as well. Rather than having to negotiate service locally in every market, IHI can use a Soracom SIM and count on the same level of service and fee structure at any of its facilities around the world.
IHI uses Soracom Air to connect a gateway at the power plant to their headquarters in Toyosu, Japan.
When the dedicated real-time diagnosis system determines that remote maintenance is required, IHI creates a secure channel between workstations on both ends using Soracom Gate to allow on-demand adjustments to the gas turbine and related systems.
Once maintenance is complete, the cellular connection is terminated while 24/7 monitoring continues.
WHY SORACOM
Secure, centrally-managed remote maintenance for facilities around the world
For IHI and their global power plant customers, remote maintenance solves a number of issues at once. With the combination of Soracom Air connectivity service and Soracom Gate for secure networking, IHI can now quickly respond to emerging conditions to keep power plants around the world operating at maximum efficiency under all conditions. The customer benefits are obvious: increased reliability, enhanced performance, and significantly lower maintenance costs.
An in-house operating software developed using the Soracom API lets IHI staff make remote adjustments on the fly even without specialized technical expertise. Many urgent fixes can be implemented without delay while teams are en route, and technical personnel are no longer required that incur costs for site visits just to perform routine maintenance functions.

FUTURE PLANS
Operational support for global customers
IHI continues working to strengthen its support offerings across the complete power plant lifecycle, from post-delivery operations support to remote management as an optional ancillary for customers already taking advantage of real-time diagnosis.
IHI expects to increase installations of gas turbine power generation facilities around the world, especially in emerging markets. With more and more installations in remote areas where physical access can be a challenge, remote monitoring and management will play a crucial role in delivering enduring value for their customers.