Is Predictive Maintenance the Ultimate IoT Solution?
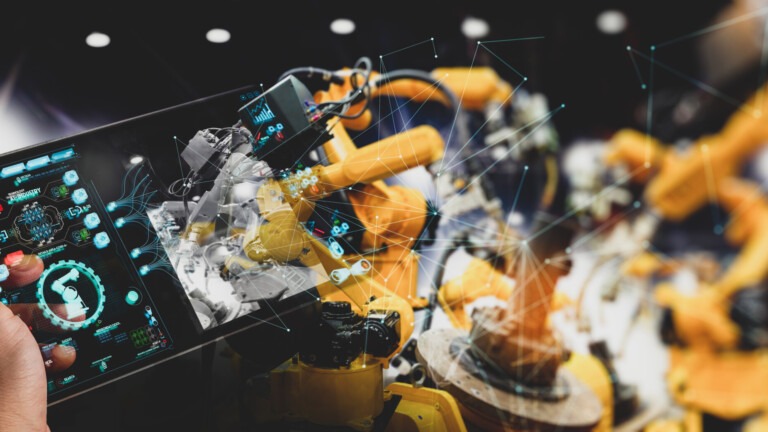
Though the implications of IoT sensors are myriad, there may be no tool more vital to modern companies than predictive maintenance. According to a report from professional services giant Deloitte, predicting failures of corporate assets can increase equipment uptime by up to 20%, improve productivity by 25% and reduce breakdowns by as much as 70%.
Beyond that, the study also found that predictive maintenance can reduce maintenance costs by 25%. This can be a lifesaver for many industries, leading to the question, what is predictive maintenance and how does it work?
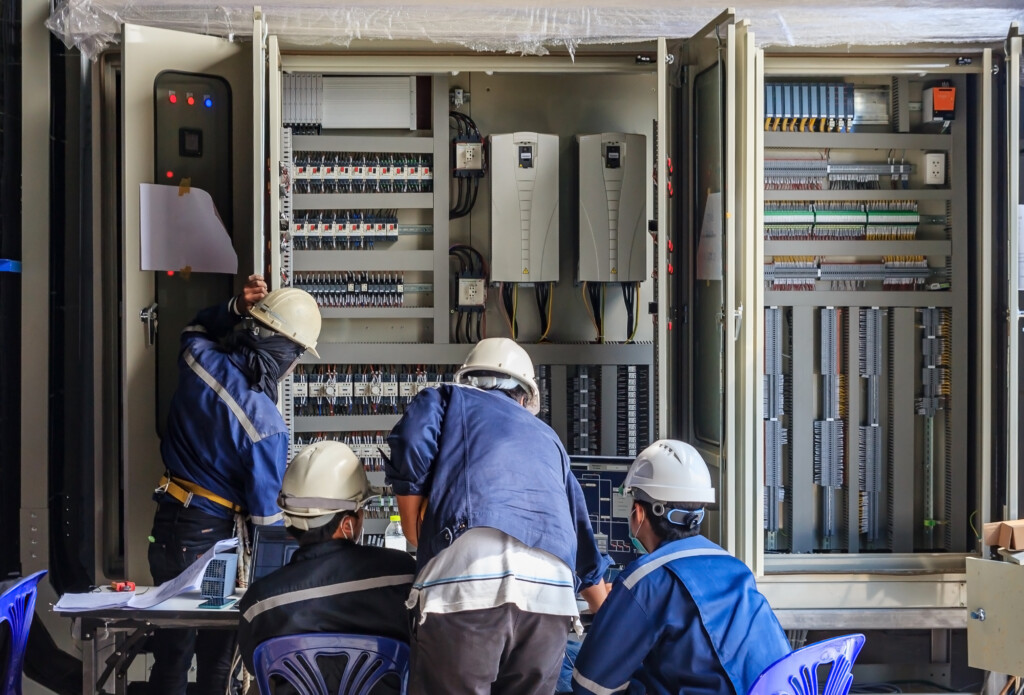
What is Preventative Maintenance?
The ultimate goal of predictive maintenance is to avoid costly downtime by successfully predicting when an asset is likely to break down and only performing maintenance when it is needed. To that end, data collected through environmental sensors and other monitoring IoT devices are thoroughly examined and analyzed to create actionable intelligence and usage patterns on the health and performance of mission-critical equipment.
By its very nature, predictive maintenance improves upon more reactive systems in which unscheduled downtime is an inevitability. A 2015 Carbonite study estimated that downtime for a small business could cost as much as $427 per minute, with medium and large companies seeing costs balloon to north of $9,000 per minute. Predictive maintenance, by comparison, is said to be up to 40% cheaper than reactive models, according to the U.S. Department of Energy.
Organizations that employ a time-based maintenance schedule may be able to avoid unplanned downtime, but the costs of inefficient asset maintenance can stack up quickly as well. The main risk is running maintenance cycles too often, leading to unnecessary spending on replacement parts or equipment for assets that could still see use. Monitoring these same assets to perform maintenance on a more efficient schedule can be up to 12% cheaper than even regularly scheduled preservation efforts.
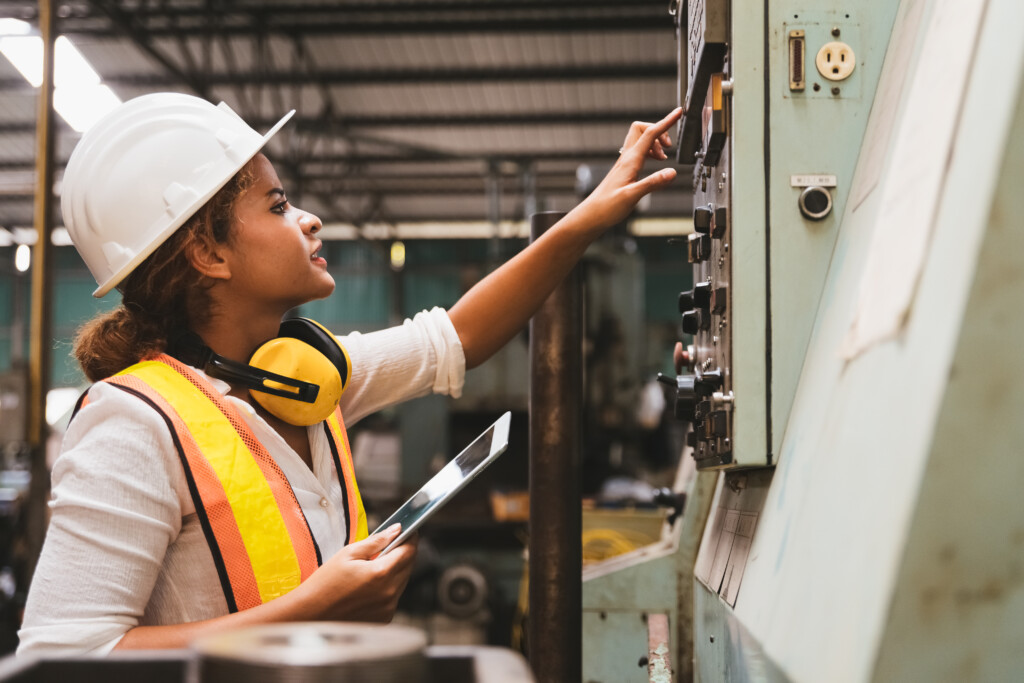
How Does it work?
At its core, all preventative maintenance begins by establishing a conditional baseline for the specific equipment to be monitored. These conditions, typically based on historical performance data or device specs, are intended to create a range for an asset’s optimal performance circumstances. This establishes a control to compare each asset’s current condition against. Those conditions are observed via IoT sensors, with that data monitored, often in real-time, for any irregularities that could suggest any potential complications.
There is a lot of variety when it comes to the kinds of sensors employed in preventative maintenance. Among the most common are:
- Temperature – Temperature is a telltale sign for machine performance, as wide variations can imply fire hazards or overworked components.
- Moisture – High levels of humidity can lead to any number of complications, like mold buildup, rust, or safety concerns from shorts in electrical equipment or slippery floors.
- Motion – Undue motion in an asset could be a sign of several potential issues, such as loose casings/housings, stressed capacitors, or off-balance motors.
- Sonic/Ultrasonic – Monitoring the sounds and vibrations of devices can be telling of their current condition, as even the smallest disparity in noise frequency could indicate imminent breakdown.
- Spectrometers – In any deployment where radiation or gas leaks are a concern, spectrometers are essential.
- Voltage/Current – Electrical shorts can be a serious risk to equipment, so keeping an eye on any unplanned electricity in an area can be key to machine upkeep.
Of course, simpler IoT solutions like security cameras are also an essential component of predictive maintenance. Being able to observe any obvious changes to an asset from a remote location is particularly invaluable to maintenance efforts in use cases that span large areas, such as oil pipelines or power lines.
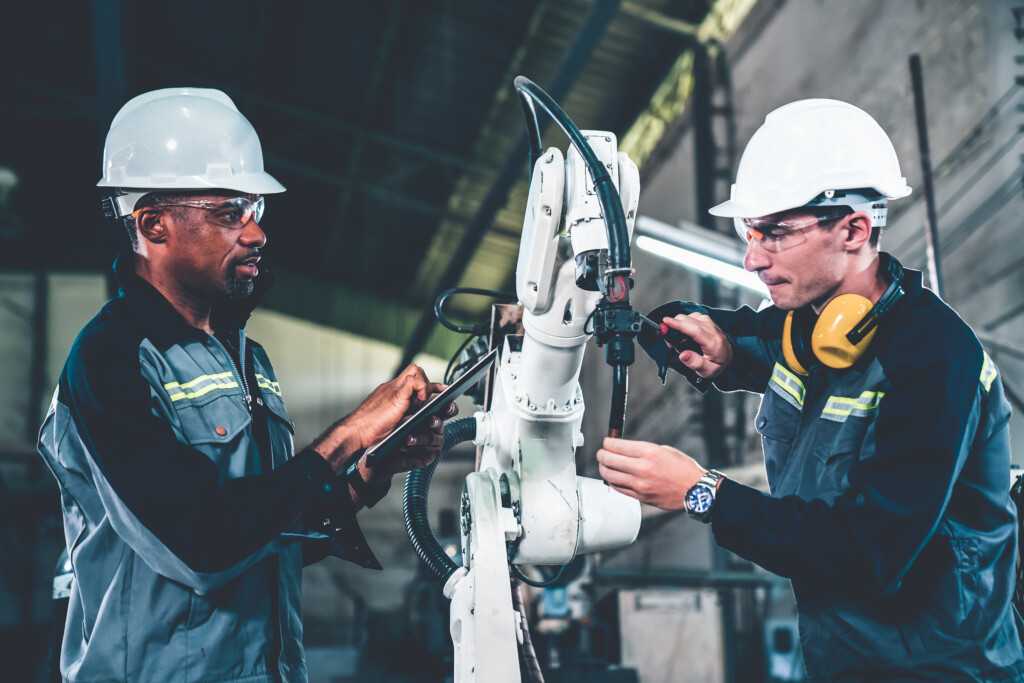
The AI and IoT Solution
Of course, issues don’t exclusively happen during business hours, so relying upon human eyes to monitor potentially hundreds of predictive maintenance data streams is typically not the most efficient. As such, many developers have employed complex AIs to analyze the fluctuations in an asset’s performance.
Artificial intelligence continues to grow and evolve, with current estimates for cloud-based AI systems placing the speed of inference at roughly 1.5 seconds. Though AI is still catching up to human reaction speeds, the tireless nature of artificial intelligence makes it a natural addition to monitoring systems. This is particularly true when one considers the large volume and diverse nature of data points that can go into monitoring mission-critical equipment.
AIs will typically run data drawn from IoT sensors through statistical models built off of historical data, run it against any parameters outlined as potential signs of degradation, and create notifications when those conditions are met. To do this, the AI creates mathematical models that compress factors such as temperature and movement into simple numerical points.
“It’s really nothing more than the good old-fashioned mathematical modeling we’ve been doing for decades,” Scott Genzer, data scientist at RapidMiner told Automate.org. “The difference is that we have the computing power to [process] massive amounts of data to find patterns, to find signal in a lot of noise that we used to do by hand.”
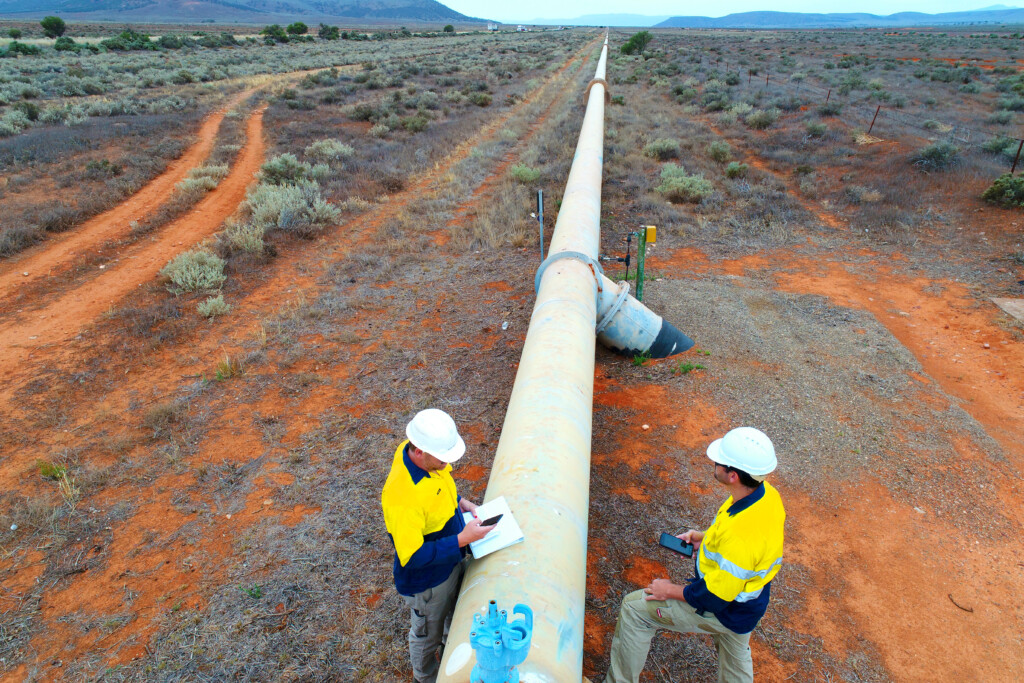
The Feature Becomes an Institution
As the concept matures, expect predictive maintenance to become even more ubiquitous. A recent report from MarketsandMarkets predicts that the market for predictive maintenance could reach a valuation of $15.9 billion by 2026.
The concept has fast become an essential element of industry 4.0, finding a home in everything from the automotive industry, to construction sites, to the oil fields. Yet the MarketsandMarkets report calls out the government and defense industries as the segment that could see the greatest investments in predictive maintenance.
………………..
Do you have questions about an IoT project? Speak with one of our experts today to learn how Soracom has helped more than 20,000 innovators deploy, scale, and secure their IoT projects.